ENCLOSURECORE Concept 3: Output
ENCLOSURECORE Concept 3: Output
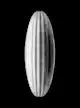
From the series: ENCLOSURECORE
Conceptual Enclosures for our AIRMADE™️ System
Concept 3 designed by Modem
The AIRMADE™️ System is not only flexible in size and configuration but also in its material output. You may know that the system can make sustainable aviation fuel, rocket fuel or methanol, but if you look a little deeper, you will see that the chemicals that make those products also form the building blocks of our world as we know it. Our third and final concept in the ENCLOSURECORE series, created by our friends at Modem, honed in on this aspect of our technology as the central idea in their work. They call their conceptual enclosure the AIRMADE™ Cocoon, playing on the fact that our system is capable of fabricating its own housing.
Based out of Amsterdam, Modem is a forward-thinking studio that operates as a hybrid think tank and design studio. Their projects feel like they are on the edge of what’s known, pushing the boundaries of design and technology. They work alongside a wide range of collaborators, from academics to technologists, anticipating “emerging signals of change and design innovative solutions in response.”
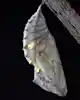
“The cocoon, or chrysalis, is the starting point of our concept. Much like a caterpillar creates its own cocoon to transform, the machine fabricates the enclosure. The machine is cloaked in flexible, woven skin that wraps around the exoskeleton. The enclosure can selectively expose parts of itself or unveil the machine in its entirety.
“The progression from feeding and growth through material production to cocoon formation is reimagined as the process of capturing CO₂ to produce a CO₂-based [material], which is then used to construct the AIRMADE Cocoon.
“Various machine configurations can be tailored to diverse contexts, from single units to factory arrangements to whole AIRMADE Cocoon farms. This extends from indoor spaces like warehouses to outdoor environments and even extraterrestrial settings.”
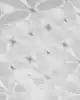
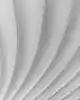

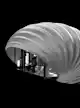
"The machine is cloaked in flexible, woven skin that wraps around the exoskeleton. The closure can selectively expose parts of itself or unveil the machine in its entirety”
- Scott Kooken, Modem
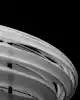
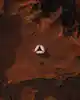
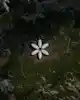
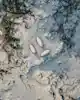
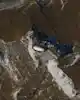
Process
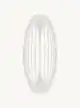
We interviewed Scott Kooken from the Modem team about their concept and how it came to life.
AC
What were your initial thoughts when we first approached you for this project?
M
If you look at what the system does, it feels like it's coming straight out of an Arthur C. Clark novel, and we wanted the enclosure to reflect that sci-fi-like promise. That was the first starting point, and the second was that from the beginning, we wanted the enclosure to be a story device—very much the same way how AIR COMPANY does their special projects: they all become story devices that communicate the mission of turning CO2 into an endless resource. Those two were the starting points that led us to approach the project as a future material study, which, of course, is a dream project for us.
AC
Where did the idea for the AIRMADE™ Cocoon come from? Walk us through the ideation behind that.
M
We liked this idea of, okay, what if the machine could be capable of fabricating its own housing in any given context, indoor, outdoor or even extraterrestrial? It led us to explore what future materials could be created from CO2 or from the outputs of the machine itself. We looked into a lot of different materials, from stone-like materials, glass-like materials, pressed panels and foams, and at one point, we were looking into yarns created from CO2.
Biomimicry can serve as a great source of inspiration, as it can provide an unexpected design solution to a problem. For example, the material Velcro was invented by this chance encounter with the Burdock Plant. It's a concept taken directly from nature and recontextualized in an industrial context, and these kinds of things are a huge inspiration for us. When looking through the book “On Growth And Form” by D’arcy Wentworth Thompson, we came across chrysalises and cocoon formations, and it perfectly fit the idea of the machine being capable of producing its housing; it was a bit of a eureka moment.
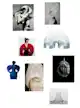
AC
We always loved that idea because when you think of a cocoon, a caterpillar goes in, and a beautiful butterfly comes out in the same way that a pollutant, CO2, goes into our technology, and a solution comes out.
M
We really liked the poetic notion of that, as it goes back to this sci-fi promise of the machine. It has this poetic idea of taking all the CO2 out of the world and turning it into something new and beautiful. We loved the magic of that.
AC
Even though the main idea was a cocoon, you did quite an extensive shape exploration. Let’s talk about that.
M
We explored a couple of design directions, from more intuitive ones to directions informed by the idea that we had for the enclosure to open. We designed more organic forms close to how cocoons look in nature to more abstract ones. The final result was almost the most simplified representation of the idea, which was very much informed by the exoskeleton and the opening system.


AC
Then there is the material itself. How did you decide what the fabric that creates this enclosure would look like?
M
We wanted the fabric to have a very visual knit texture to communicate the story of the CO2 yarn. A 3D knit ended up being the most logical approach.
AC
What steps did you take to bring this enclosure to life?
M
It was a very eclectic process. We spent a lot of time in the concept phase, going through a lot of books and research, trying to move outside of the digital space. The design process was a hybrid between 3D and analog processes as different people within the team work in different ways.
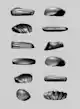
AC
What was the most challenging part about making this conceptual enclosure?
M
Combining the exoskeleton with the multi-opening system and finding the right balance between them was the biggest challenge. When moving from the initial sketching stage and trying to make the different approaches work from a functional point of view, you run into a lot of different challenges.
AC
Let’s talk about the thought process behind the openings in the enclosure.
M
Quite early on, we landed on the idea of the enclosure system being multifunctional and having two different opening systems: smaller ones for quick and easy access into certain parts of the machine and another system that would reveal the whole machine.
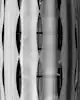
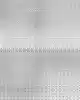
AC
We know the enclosure has a fun hidden design element. Care to share?
M
When using a 3D knit, you have full control of how the actual pattern of the knit ends up looking. When we were deciding what that would look like, we were also working on the different setups of the machines across various contexts and purposes. At one point, we created this triangle shape with three of the cocoon enclosures together, and we thought, hey, the whitespace looks like the AIR COMPANY logo mark, so we played around with using the shape of the cocoon and that setup as a pattern on this knit. It was a happy accident.
AC
Definitely. It was such a nice surprise to see—an elevated design touch.